Why is Antiresonance driving good and why could it be bad?
Why is Antiresonance driving good and why could it be bad?
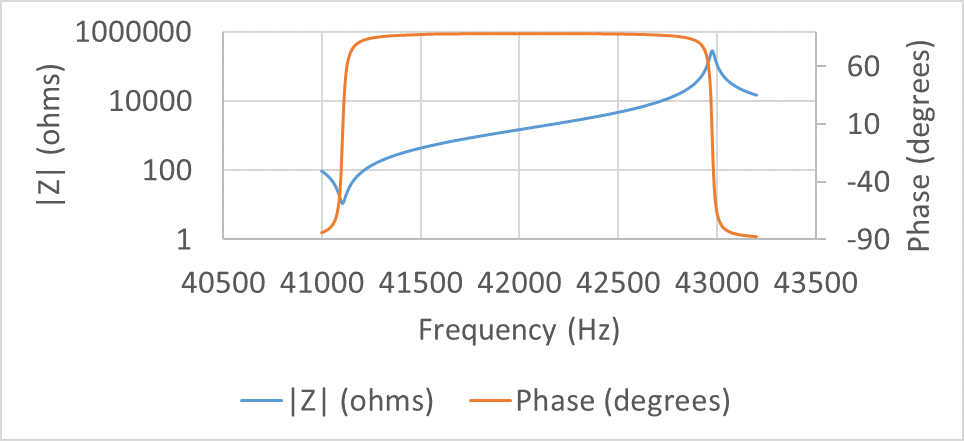
But what about antiresonance? Many years ago, as a mechanical engineering undergrad doing piezo device research, I was completely confused about the existence of the antiresonance phenomenon. That is because for 99% of transducers, the antiresonance effect is a pure electrical phenomenon. The antiresonance can be described as the frequency where the direct piezo effect is creating current at an opposite phase to the intrinsic capacitance of the transducer. That means mechanically generated current is canceling with capacitive current, thus making the current draw of the transducer very small giving it a high impedance.
Is high voltage drive really that bad?
Piezoelectric devices are voltage driven, and thus there is no “displacement peak” at the antiresonance frequency. Actually, if you were to hold voltage amplitude at a precise level, you would not find any distinguishing feature from a displacement vs frequency response at the antiresonance frequency.
If the displacement is smaller at anti-resonance in comparison to the resonance frequency, why would we use anti-resonance at all? Most commonly, ultrasonic welding equipment uses anti-resonance, so why should those applications use antiresonance if it takes more voltage to drive the transducer to the desired mechanical output.
The last paragraph was “charged” with an assumption (no pun intended). The assumption is that high voltage is not desirable. The four universal reasons why high voltage (500V+) is undesirable is
(1) Dielectric heating
(2) Increasing the potential for arcing
(3) Safety risk
(4) Risk depoling ceramic if negative voltage is applied.
These problems can be combated by:
(1) Dielectric heating can be combated by using hard PZT (low dielectric loss)
(2) Good mechanical and acoustic design, conformal coating, applying insulation, and increasing the number of piezo elements can decrease the likelihood of arcing
(3) For non-consumer applications, proper grounding can ensure user safety
(4) A positive DC bias can provide relieve from negative voltage
Why is antiresonance a good thing?
We just discussed why antiresonance and it’s necessity of using a large voltage in actuator applications is not necessarily a bad thing. But why is it a good thing? What benefits does antiresonance driving provide?
Antiresonance presents a high electrical impedance to the electrical driver. When a transducer is loaded, the antiresonance impedance drops –voltage delivered to the piezo is still constant because the impedance is still high (although lower than before) the amount of power delivered increases. Going back to Ohms law, V=IR, the R drops, and therefore the current and hence power delivered to the transducer increases. What is happening is that the transducer output power is self-regulating without the need for a high-performance feedback circuit. When the transducer is loaded, more power is instantaneously required to maintain the oscillation amplitude -hence, using the anti-resonance frequency drive promotes an analog method of adjusting power according to the load presented to the transducer.
Antiresonance drive can also be thought of as oscillation amplitude correlating directly with voltage, whereas at resonance the oscillation amplitude correlates to current. Because electrical driving circuits operate on a controlled output voltage level scheme, and not constant current, utilizing antiresonance makes the electronics and control algorithm simpler.
A proper transformer is all you need to efficiently step up your low voltage driver to become an antiresonance driver. If your application requires a lightweight electrical driver, this method may not be possible because transformers are large in comparison to other electronic components.
Please reach out if you have comments and questions on this article (husain@ultrasonicadvisors.com). I’d love to hear from you.